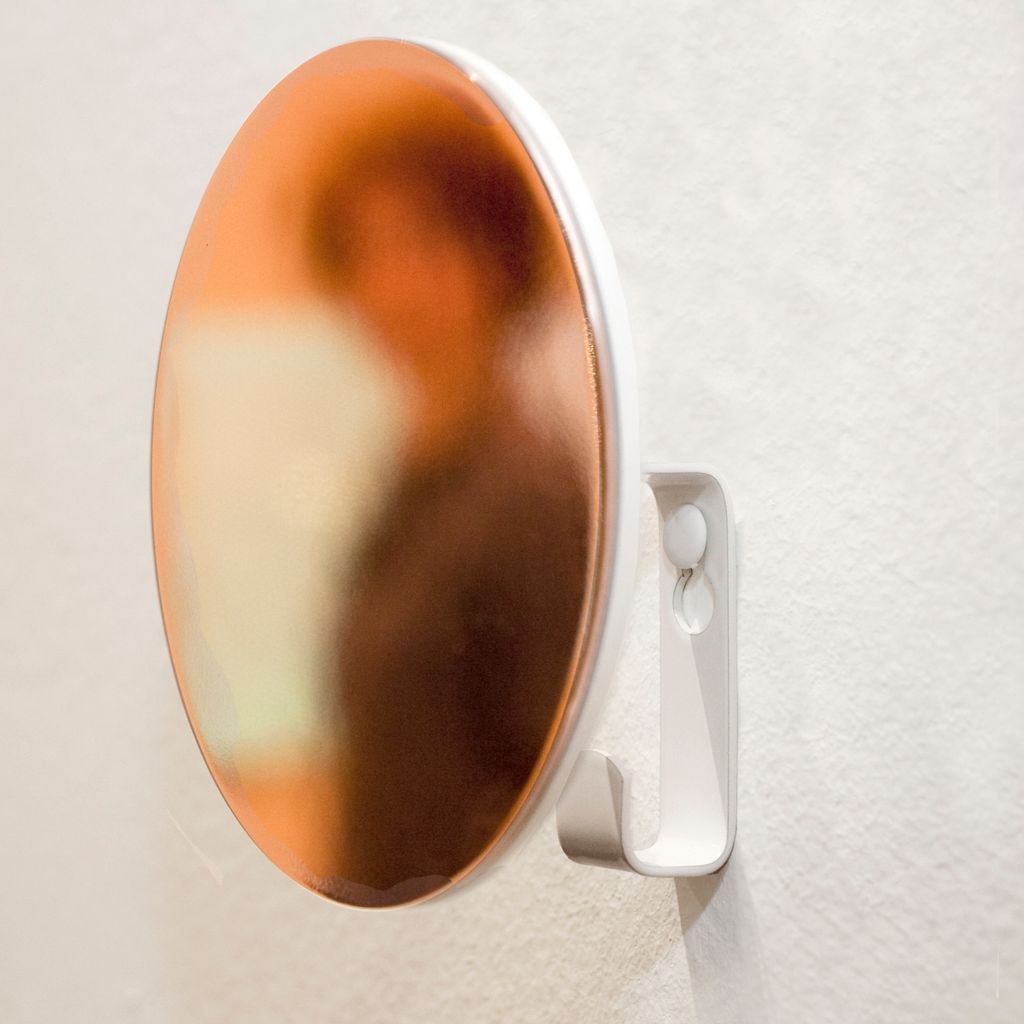
Architect, teacher and trainer, Susanna Campogrande wears many hats. Consulting in industry innovation for Wood.be is what best characterises her, considering her expertise in innovative materials, resource sharing and design. A sector where the adaptation to the ecological transition is becoming increasingly clear.

Where does your multidisciplinarity come from and how does it allow you to respond to very real questions and needs?
My architectural eye allows me to put ideas into context before they are designed, to get to the point. My training in the profession at the Polytechnic University of Turin allowed me to understand how a complex project is created and managed in the sphere of housing, fashion and even the automobile, from the scenarios of use to production through the choice of materials. After graduation, I lived in Paris for ten years. I coordinated the Innovathèque: the first material library for design professionals to be created in Europe. I then moved to Brussels. Since then, I have had the opportunity to deliver several projects between interior architecture and design, alongside the agency, Arch & Types, and the creative studio, Aller-Retour (which we founded with Lise Casalegno Marro).
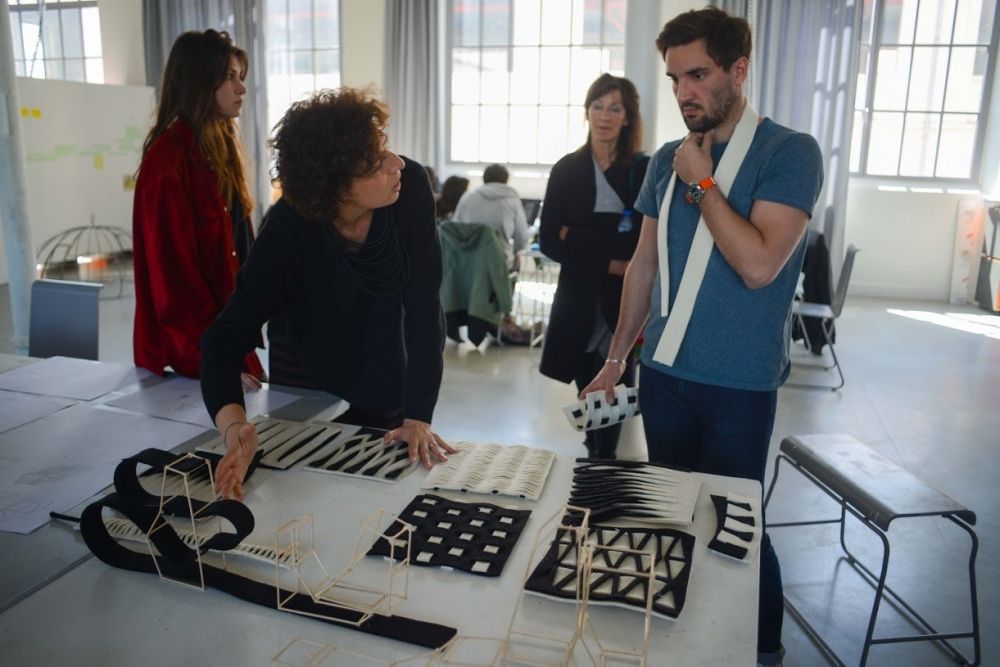
You also teach the latest in design and textile design at the Royal Academy of Fine Arts in Brussels (ARBA-ESA).
In Brussels, I had already had the opportunity to teach at the École nationale supérieure des arts visuels (ENSAV) de La Cambre and at the College of Art & Design (CAD). At ARBA-ESA, I am part of the teaching team for the textile design programme for the follow-up to the Masters and I give a transversal course on current design issues. The audience which I address does not necessarily have an overview and a specific view of the world of the design industry during their studies. This is what interests me in order to be able to talk about innovation in theory and in fact.
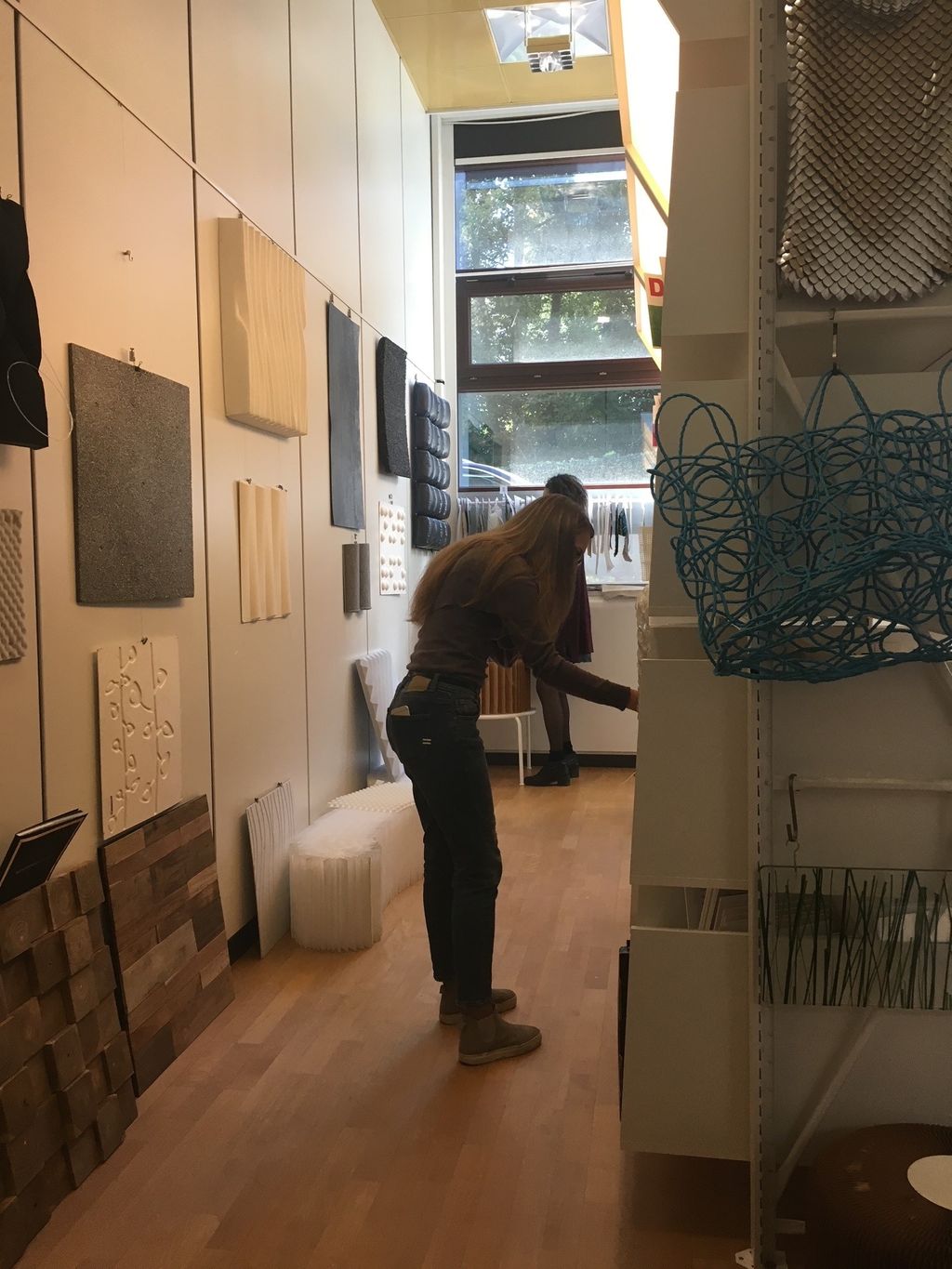
What did you learn at the Innovathèque, an “innovation incubator” before that word existed?
That technology and new materials allow for profound and sustainable innovation. The materials library is a place where samples of innovative materials are sourced, selected, referenced and displayed, outside the context of their use, in order to inspire and stimulate technological transfer (the appropriation by an industrial actor of a technology used by a public or private actor). It brings together a public of designers, architects, specification producers and entrepreneurs who come and seek ideas for their projects. It is this process of discovery and exchange which relies upon potentially innovative components which I try to implement in my activities so that they can lead to results and, quite modestly stated, bring about the evolution of the world of production.
How do you support your students now?
I draw upon my experiences, my practice in the institutional and business worlds, in order to provide students with a key to understanding how to innovate today. Is a project technically feasible, financially feasible, does it depend on a new patent, access to sourcing close to or far from the production site? I attempt to clarify the current trends of which many students are already aware, and to provide answers to these questions. I train them in “circular culture” and direct them, for example, towards the recycling of materials or the creation of new ones, because even with the advent of digitalisation and the resulting dematerialisation, the material forms the basis of all tangible creation.

What do companies think?
Industry is interested in the new generation and their approach to things and are always ready to train these new faces but often fear not having the right tools at their disposal to innovate, or a vision which is sustainable in the long term. Marketing does not have the answer to everything. Today, new companies are springing up to meet the growing demand for eco-friendly products, and many others are adapting. Several success stories are to be noted, which is motivating, but the era of high consumption in which we find ourselves still benefits a lot more from greenwashing than from real adaptations and changes on the part of the so-called polluting industries.
Fashion is often blamed for its artificiality but recently there has been a paradigm shift within it and this is thanks to its thirst to create through the use of textiles.
Yes, but large-scale eco-design requires certain economic means. Nothing is impossible: just look at Adidas, which is experimenting with trainers which are just as efficient as their usual models, but entirely circular; 100% recyclable and reusable once used so that they can be reduced to granules for making new shoes.
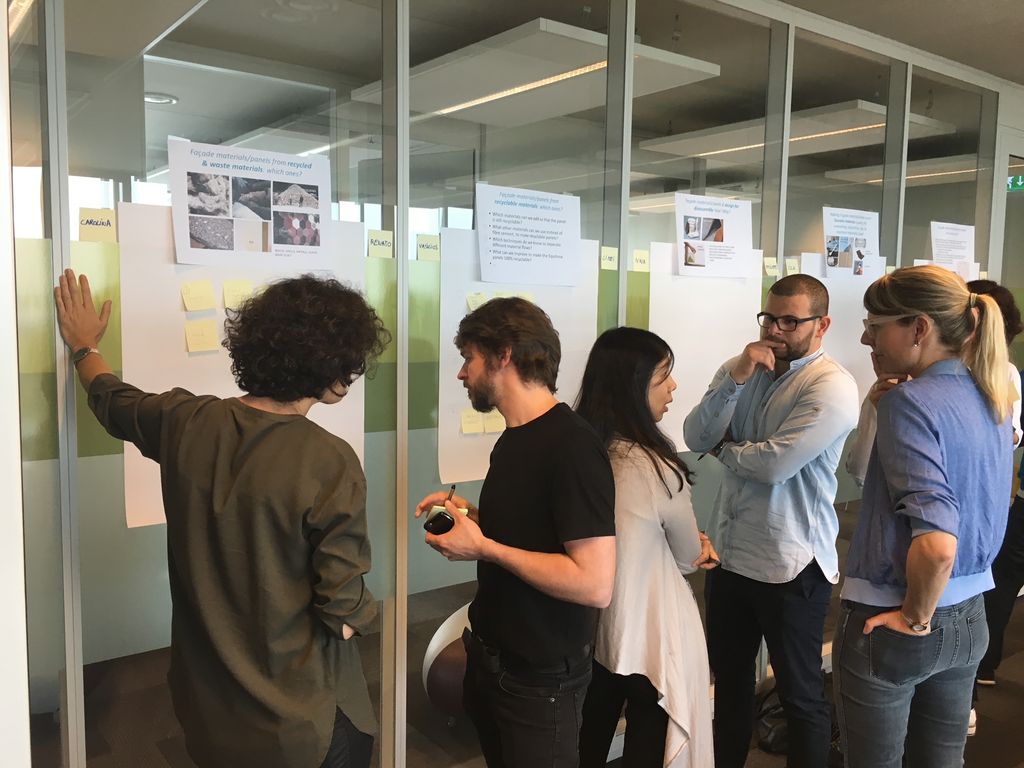
How is this cradle-to-cradle approach being implemented in the housing sector?
This mode of industrial production, which creates a positive impact upon nature but also upon humans and their accountability within society, making the end of a product’s life an asset for both anti-waste and innovation, has its own label called C2C. This approach is rather complex (and expensive), but feasible. Some of the existing business models do not allow for this type of production and need to be completely revised. Sometimes products have been eco-designed and are repairable, but flaws in the company’s business model do not allow for this circularity.
Has e-commerce made this type of initiative more visible?
It’s all a question of scale, according to the size of the companies, their budgets and their influence. Renting products and the sale of second-hand products by the brands themselves (such as what IKEA offers), will also open the way for other multinationals which were previously reluctant to get involved. It remains for the infrastructures and administrations to adapt, because the modes for production and sales of this type rely upon chains of various interlocutors and upon several territories, which can be unmanageable for human-sized companies. For them, the issues of material and product traceability and reverse logistics are crucial.
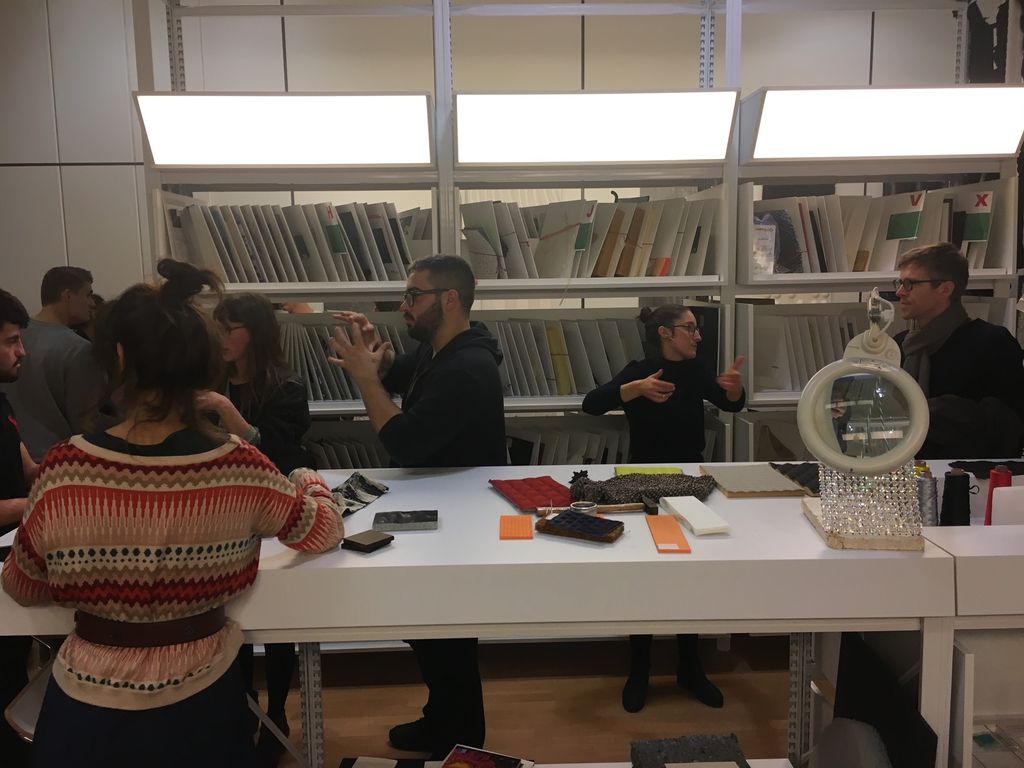
How do the services which you offer help raise awareness among start-ups, small and medium-sized companies?
At Wood.be, we support projects which are primarily Belgian and have a sustainable ambition in the wood and furniture sector. The themes of most interest to manufacturers at the moment are the circular economy and digital transformation, all in support of the optimisation of production of course. In a word, we are supporting the transition to Industry 4.0. I work in the Innovation team as a project coordinator and facilitator of working groups. We study the evolution of the furniture market and propose reports regarding trends and thematic monitoring.
How does this translate from design thinking to action at your end?
The technique known as design thinking is only a working method like many others. In my case, when I lead workshops using this technique, I put into practice my knowledge of the furniture and construction sectors. I recently conducted a workshop with a company in Liège specialising in construction using wood. The proposal for a sector-specific eco-design guide and this workshop generated several new ideas to implement in this respect.
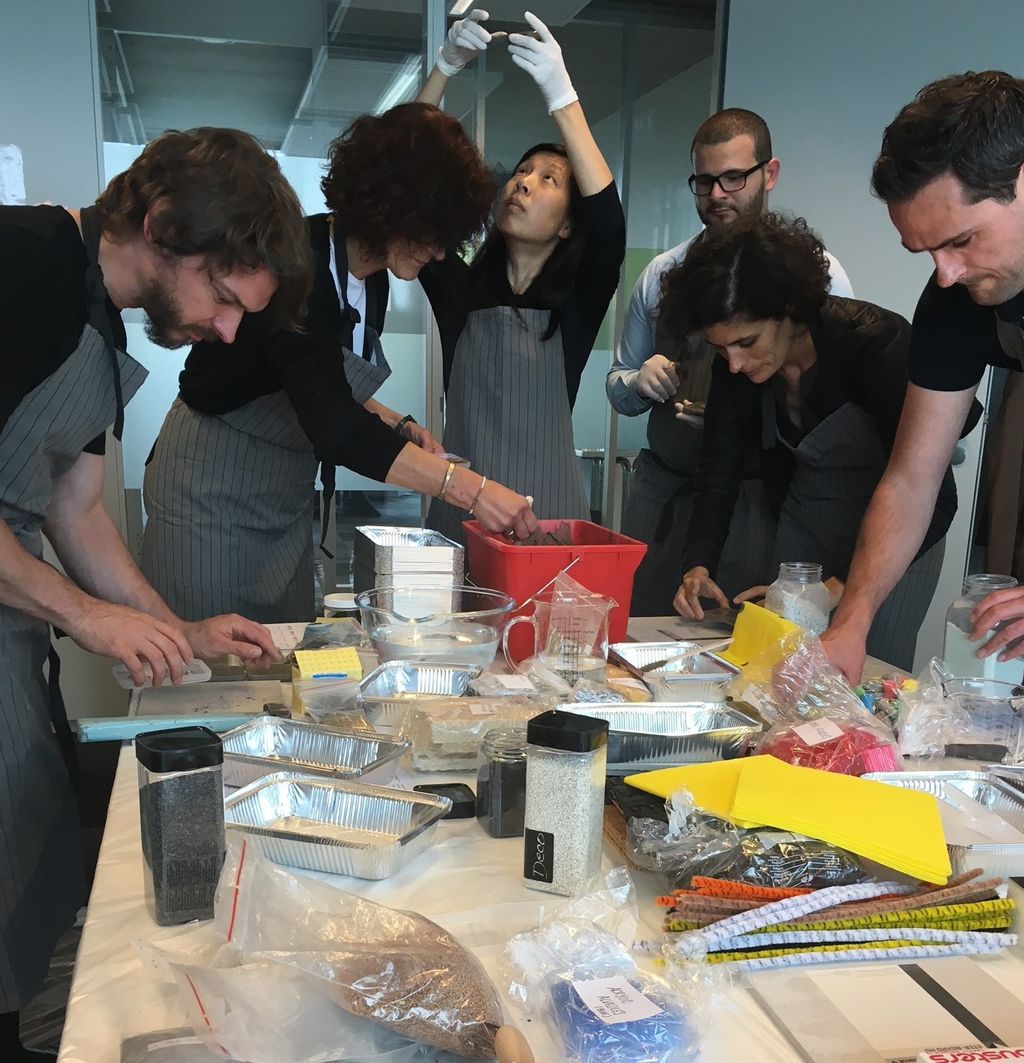
How do you react to the recent cancellations and postponements of several trade shows?
This is due to several factors. Firstly, more and more sales are made directly by the brand (this is the case for new brands depending only on their e-shop, without any external point of sales). Also, the last intermediaries between them and the consumers have been considerably reduced: communicators, commercial agents, but also showrooms and therefore trade shows and fairs, which will certainly accelerate and anchor a new reality with reinvestments towards marketing, communication and purchase-sale supports, mainly digital, and a valorisation of events which is more local than global and targeted. But nothing will ever replace the human exchange between apprentices, emerging brands, established designers and industry behemoths from around the world who meet at these international events, such as the Milan Design Week or Maison&Objet in Paris. Face-to-face relationships allow us to establish sustainable human links, beyond the pleasure of exchanging ideas over an aperitif or a coffee.
So how can industrial production be made to evolve sustainably through innovation?
Through dialogue and human contact, certainly.