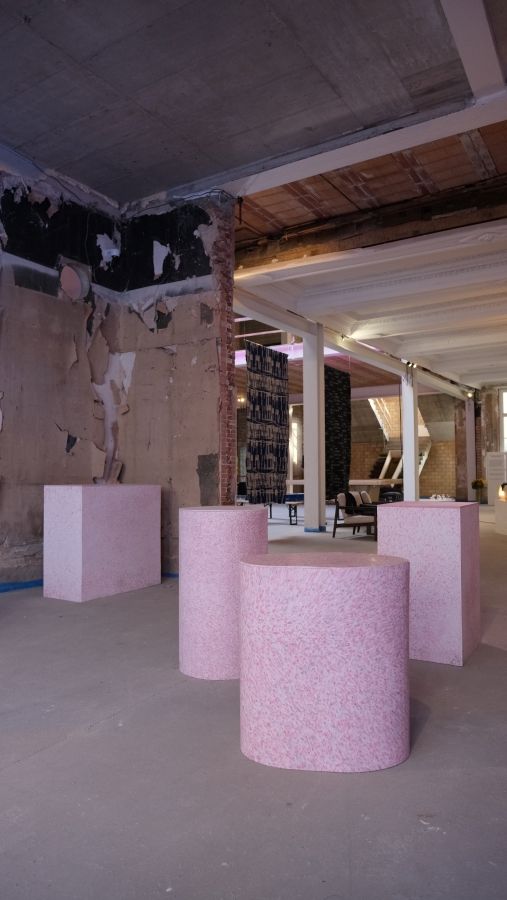
Local, recyclé, durable et innovant, les atouts du plastique tel que valorisé par Bel Albatros sont nombreux. Fondé en 2018 par les entrepreneurs Guilain Sevriere et Elisabeth Trivière, la société continue de se développer.
La durabilité, la transparence de sa production mais aussi son engagement sociétal et environnemental séduit les designers, comme Lionel Jadot, avec qui Bel Albatros refait les chambres de l’hôtel Jam à Bruxelles, les créatifs travaillant sur les jouets pour enfants Combo Toys. Ainsi que des grandes entreprises comme la banque Triodos, et des artistes plasticiens tels que Jean-Baptiste Bernadet et Sammy Baloji, pour une œuvre dans l’espace public. Leur produit – la plaque en plastique recyclé – propulse le recyclage de déchets de matériaux composites sur le devant de la scène et donne matière à agir. Elisabeth nous en dit plus.
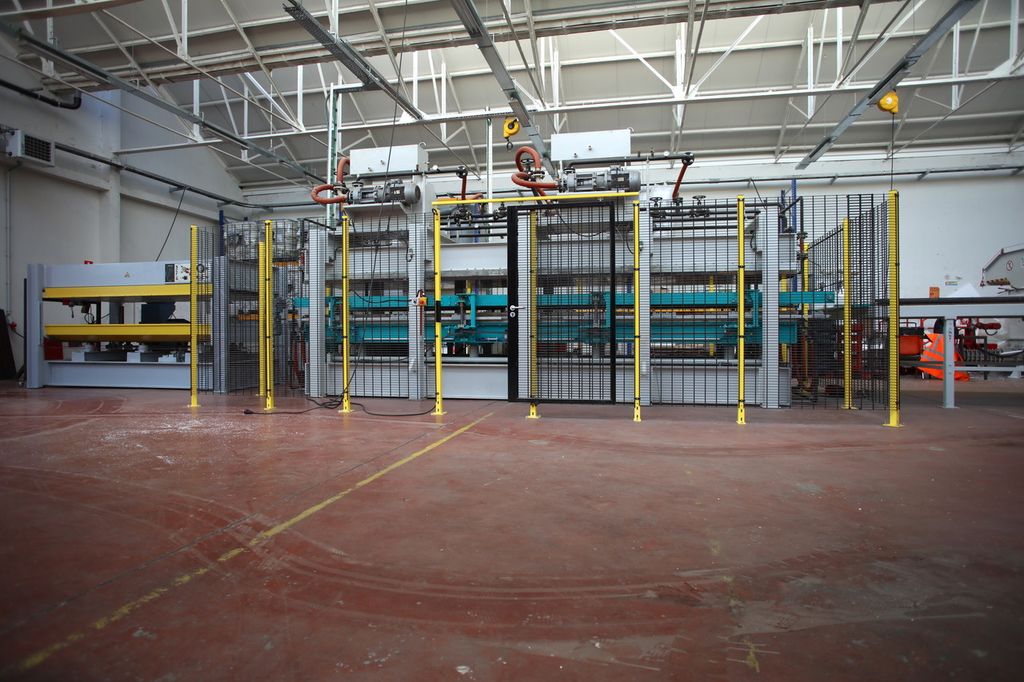
Qui se cache derrière Bel Albatros ?
La société part d’une idée et d’une envie de Guilain. Elle présente une véritable dynamique familiale, tant au niveau des associés que des employés, incluant également deux frères au sein de l’équipe (bien qu’ils ne soient pas de notre famille). Depuis deux ans, on a dans notre équipe un groupe qui réunit des designers, un ingénieur et un artisan.
À quelle génération appartenez-vous tous ?
Guilain va avoir 40 ans, j’ai bientôt 32 ans et nos designers sont tous plus jeunes, entre 25 et 30 ans.
Quelles ont été les prémisses de Bel Albatros ?
Guilain, qui a fait une école de commerce, s’est retrouvé à être commercial dans une boîte d’innovation et de dépôt de brevets. En grand touche-à-tout, il a continué de bricoler tous les week-ends et a commencé à réaliser des prototypes pour des clients. Pour ses projets, il s’est tourné vers des fab labs et il est devenu fab manager d’un des ateliers de fabrication bruxellois, Citifab 3. Il a ensuite créé un fab lab avec un ancien collègue.

Comment en êtes-vous arrivé à vous intéresser au plastique et à sa seconde vie ?
Chaque fab lab a habituellement son pôle de spécialisation selon les matériaux : bois, métal… Et il y avait, il y a quelques années, les imprimantes 3D de plastique. On s’est rendu compte que le plastique générait beaucoup de déchets, contrairement au bois, qui peut se réutiliser pour se chauffer, ou au métal, qui est bien recyclé. De ce constat, nous avons travaillé sur un premier projet open source, qui s’appelait Precious Plastic ; des petites machines DIY [do it yourself, NDR] qui permettent de recycler le plastique. Notre premier client fut le festival We Love Green à Paris, pour un chapiteau éphémère. On a dès lors pensé que l’on pouvait vendre plusieurs disques de plastique recyclé générés avec ces machines fabriquées maison mais ça ne s’est pas passé comme ça… On a été voir Belgiplast, l’un des derniers injecteurs bruxellois qui existe. Il a accepté que l’on mette du plastique recyclé injecté dans leurs machines, malgré les risques de les détruire. Donc, on attendait, voire on dormait, devant les machines, et on les arrêtait dès que la buse d’injection se remplissait ! Tout cela a participé à notre histoire et nous a éclairés.
Après avoir testé cette première phase – l’injection de plastique recyclé – quel était votre challenge ?
Le défi est de valoriser au maximum le plastique recyclé et de changer les mentalités autour de celui-ci. Il s’agît de passer de la vision jetable du plastique à faire de la durabilité du plastique une force. Mais, si obtenir la confiance d’un client n’est pas compliqué aujourd’hui (ils sont ouverts), un moule d’injection coûte près de 80 000 euros ; un important investissement financier… Il y a aussi l’idée courante qu’il est difficile de considérer un objet fabriqué en plastique en série comme pérenne et non jetable.
Quel fut le déclic pour parvenir à produire des plaques de plastique recyclé ?
À force d’échanger avec nos clients, on revenait au même concept : faire une plaque avec moule simple et pouvoir concevoir des objets en trois dimensions à partir des découpes de cette plaque. Un jour, une opportunité s’est présentée : on a pu acheter notre presse ! On a donc déménagé notre atelier chez Recy-k la veille du premier confinement dû à l’épidémie de Covid-19 !
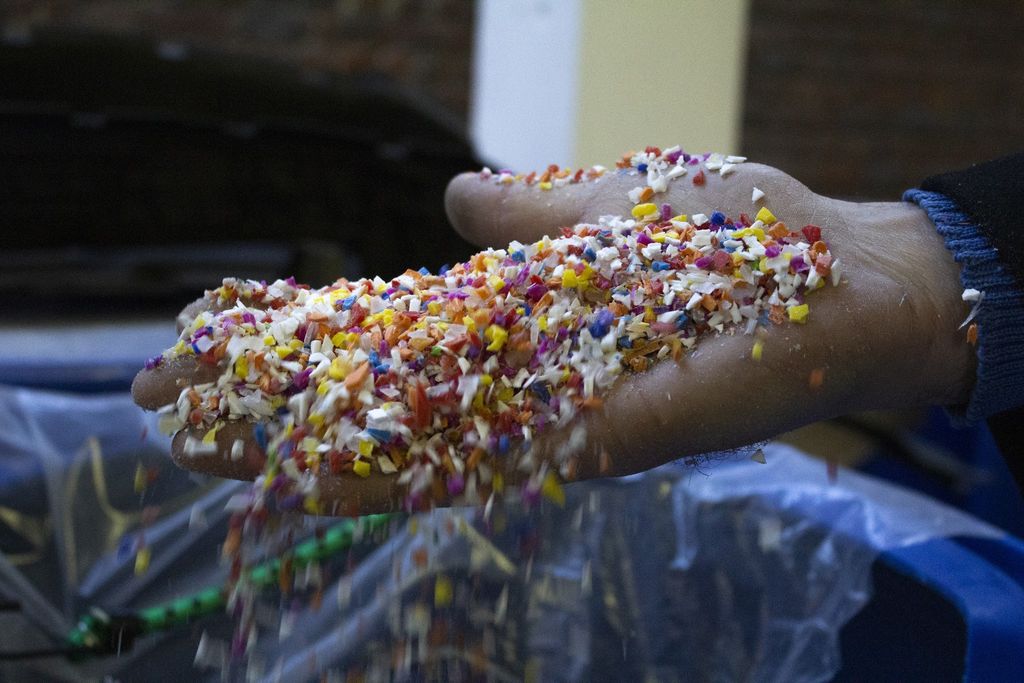
À quoi ressemblent les plaques que vous produisez depuis ?
Elles forment un nouveau matériau. Les plaques sont attrayantes, colorées, et elles ont des finalités similaires à ce qu’il est possible de faire avec de la céramique ou encore du marbre : des objets en trois dimensions et du volume. On a commencé à vendre nos premières productions de plaques très rapidement, après une phase de mise au point des machines pour qu’elles puissent servir nos missions : réutilisation, réparation, réemploi et recyclage.
Bel Albatros est-il unique en son genre ?
Dans la production de plaques en plastique recyclé à Bruxelles, nous sommes relativement nouveaux. Nos évolutions en matière de la plasturgie restent encore inédites. On reste outsiders du milieu de la plasturgie avec qui nous sommes en contact et avec qui nous échangeons sur des problématiques techniques : en plus de l’injection, on fait aussi de la compression (ce qui reste peu vu dans la plasturgie classique). La plasturgie est une science en soi avec la préparation et la température de la matière, sa fusion, sa viscosité – autant de paramètres qui sont pris en compte… Aussi, nous travaillons avec un plastique impur, ce qui signifie que chaque « fournée » change la donne, tant au niveau du rendu final de la plaque que de la production en elle-même.
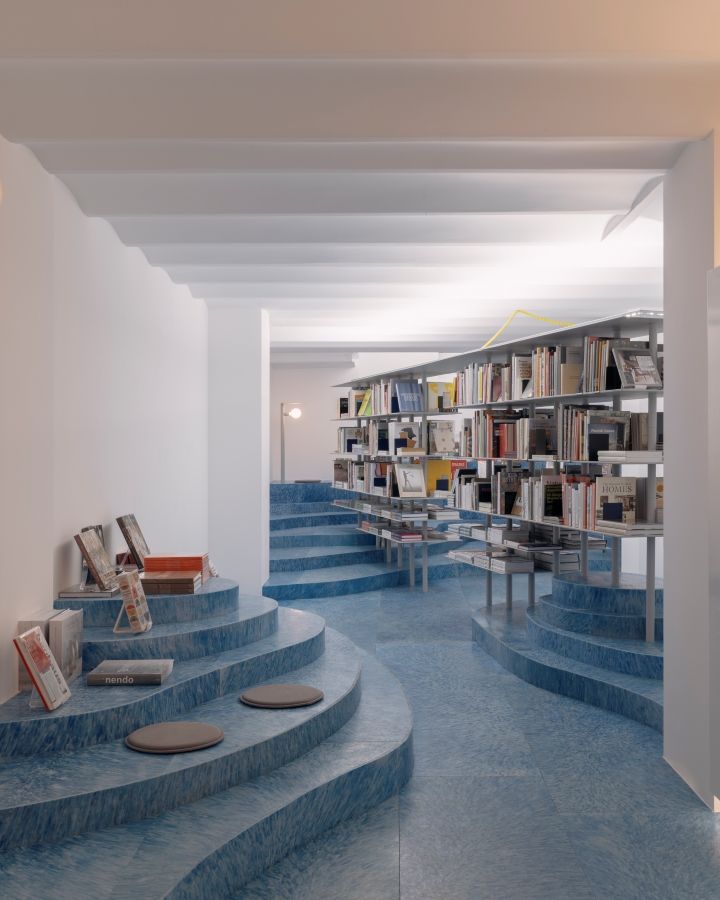
Comment vous positionnez-vous dans ce marché naissant de la plasturgie écoresponsable ?
Nous sommes avant tout des fabricants. Nous travaillons pour les créatifs, les designers, les architectes et les entreprises. On réalise leurs idées avec notre outil. À Bruxelles, on a un concurrent qui peut créer des plaques plus petites et fait ses propres objets (porte-savons, planches à découper…). On a quelques concurrents européens dans la production de plaques à partir de déchets plastiques. Ils fonctionnent à une échelle industrielle. Nous y arrivons, mais pas à pas.
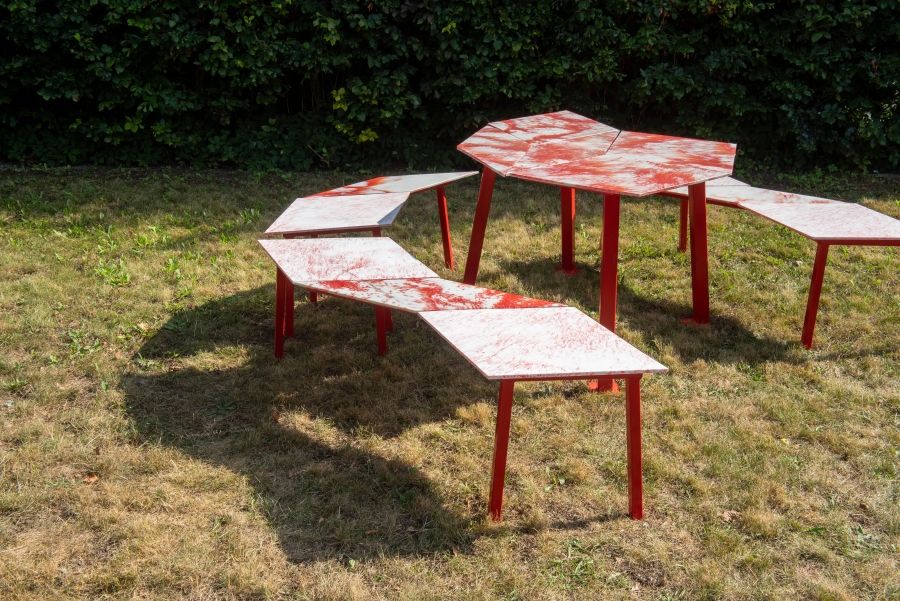
L’une de vos spécialités est la couleur sur-mesure des plaques que vous proposez.
Oui, tout comme des plaques de grande taille d’un mètre sur trois mètres en polyéthylène (et en polystyrène prochainement). Nos couleurs sont sélectionnées par le client mais il arrive que de nouvelles couleurs soient générées à partir des copeaux dûs à la découpe des panneaux.
Nous re-granulons donc ces copeaux pour produire de nouvelles plaques. Nous sommes donc parvenus à proposer une gamme sur-mesure et une gamme de stock qui nous permet de répondre à de plus petites commandes.
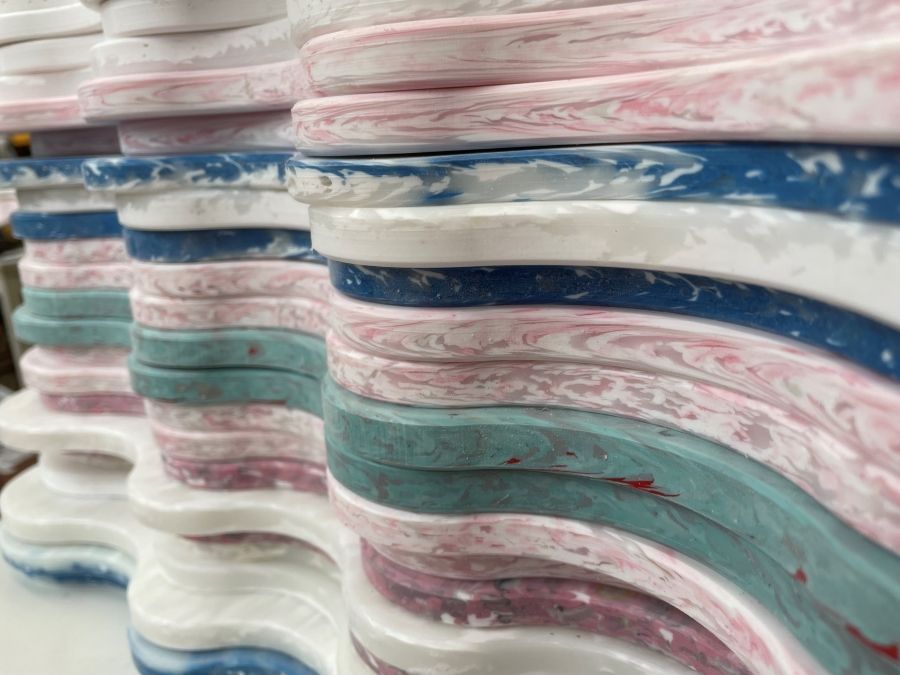
Quelles évolutions de comportements à propos du plastique recyclé observez-vous ?
La résistance au feu est une question qui nous revient souvent. La réponse est qu’il réagit comme du bois. Il peut y avoir une marque à plus de 130 °C mais la matière peut être ensuite poncée. L’apparence du plastique recyclé est proche de la pierre naturelle (terrazzo, voire marbre) mais il est doux au toucher, élément primordial pour nombre de personnes. Les nouvelles générations de designers à la recherche d’éco-matériaux apprécient le plastique recyclé, car il est un matériau responsable qui est accessibles et avec des propriétés techniques adaptées à plusieurs types d’usages : résistance à l’eau, aux acides et aux rayons UV, imputrescibilité, polissable, thermoformable et soudable, usinable… Notre plastique fait parler de lui !